FULL LIFE
ACHIEVED FOR CYLINDERS
UP TIME
SIGNIFICANTLY INCREASED
COSTS
SAVED ON REPAIRS
The Challenge
HMG’s customer Newcrest Mining had an ongoing issue with OEM manufactured hydraulic cylinder eye cores cracking during operation on their excavators.
This unexpected component failure had occurred on excavators across various mine sites and was causing significant downtime for the machinery, loss of production costs and repair or replacement costs.
Newcrest Mining had sent HMG several cylinders in for repairs with a variety of stress-related breakages from cracks to complete severance of the eye cores.
Although the machinery was being used in conjunction with OEM application standards, it was clear that this area of the cylinder was fatiguing quicker than the rest and therefore an upgrade was required.
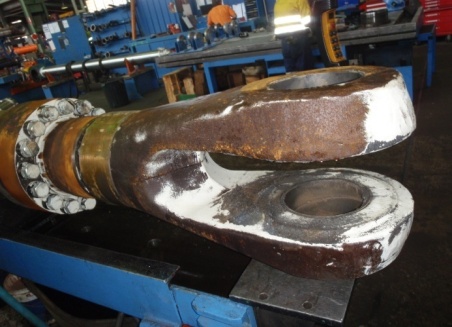
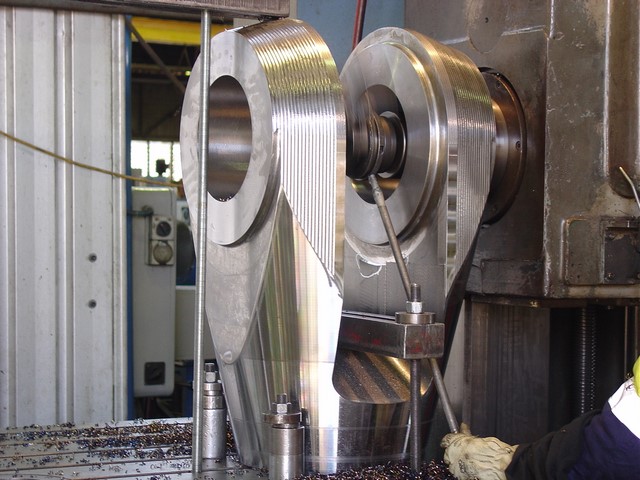
The Solution
HMG recognised this was an ongoing issue and developed a solution to produce stronger eye cores for excavator cylinders.
The solution involved the manufacture of eye cores using solid billets.
HMG’s Engineering team designed eye cores with the aid of CAD program to ensure seamless compatibility with the rest of the cylinder and its arrangement group. These design specifications were then programmed into HMG’s state-of-the-art CNC machinery, and were then machined and profiled into shape.
The component was then ready to be welded to the end of the barrel and the rod eye core is ready to be bolted onto the retainer.
The material utilised is Q & T carbon steel which provides superior material properties against castings.
To date there have been no failures of eye cores that HMG have manufactured from solid billet.
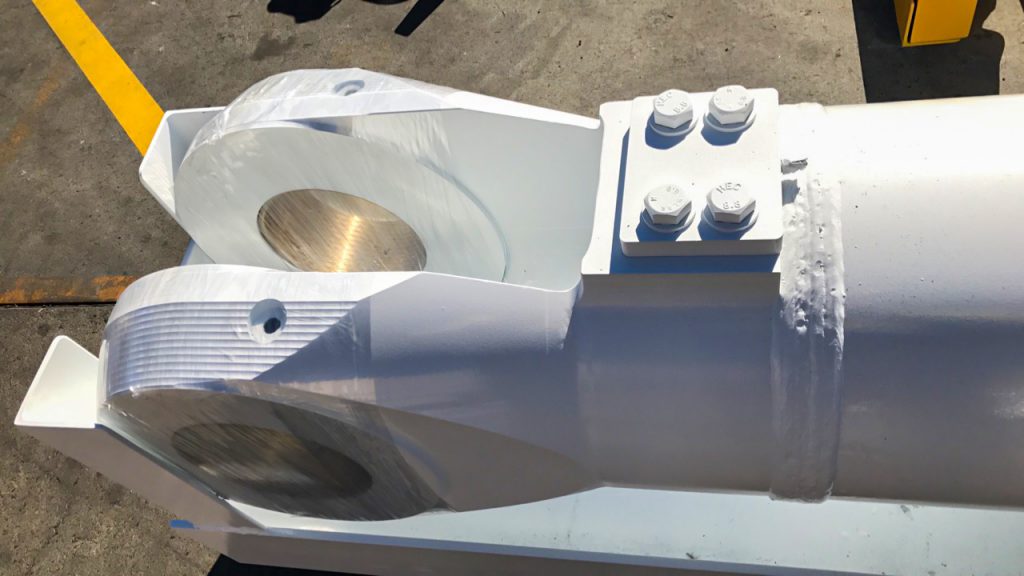