20+ DAYS
AVERAGE HYDRAULIC CYLINDER TURNAROUND
23
PARTS REPAIRED
CUSTOM
CYLINDERS MANUFACTURED
The Challenge
Our client, Hall Contracting, were conducting a dredging operation in Spoilbank Marina, WA where they were using a Liebherr P9350 backhoe dredge to relocate more than 120,000m3 of material over a six-month period.
This job was part of a larger project, and as such, any machinery downtime would be detrimental to the project timeline as well as having significant financial implications. Recognising that the project was vulnerable to significant revenue loss if the P9350 backhoe were to suffer a hydraulic cylinder failure, Hall Contracting contacted HMG to supply a new set of hydraulic boom cylinders to keep on standby for emergency replacement.
Hall Contracting requested these cylinders be manufactured and tailored specifically to withstand the harsh marine environment in which they would be operating.
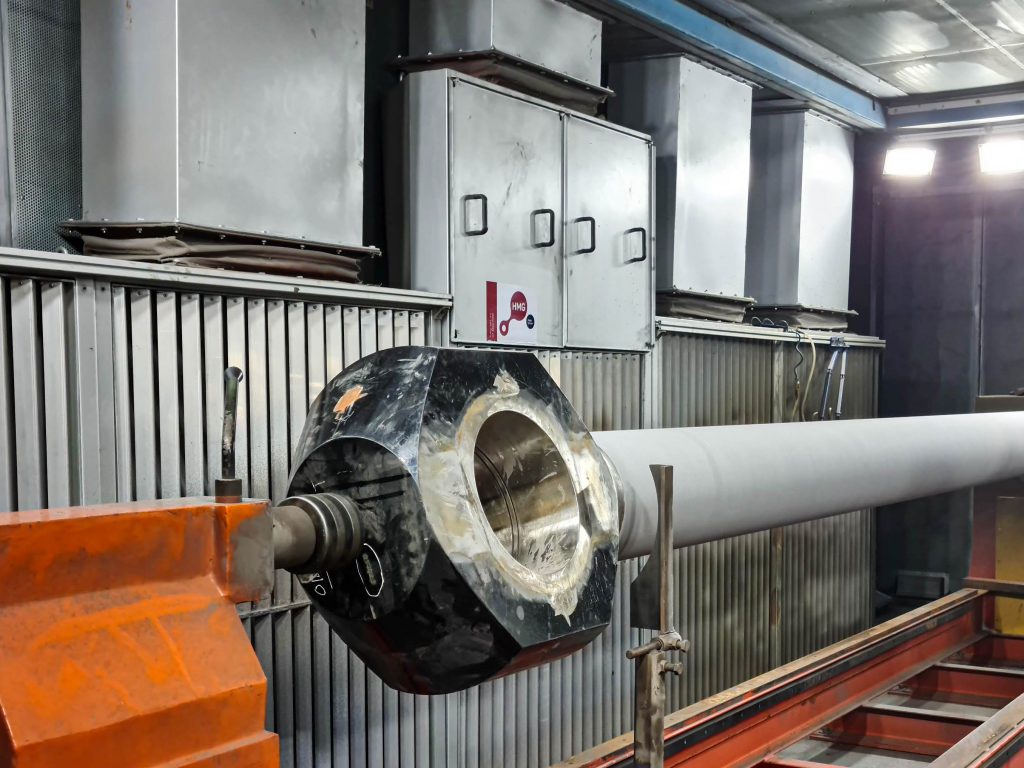
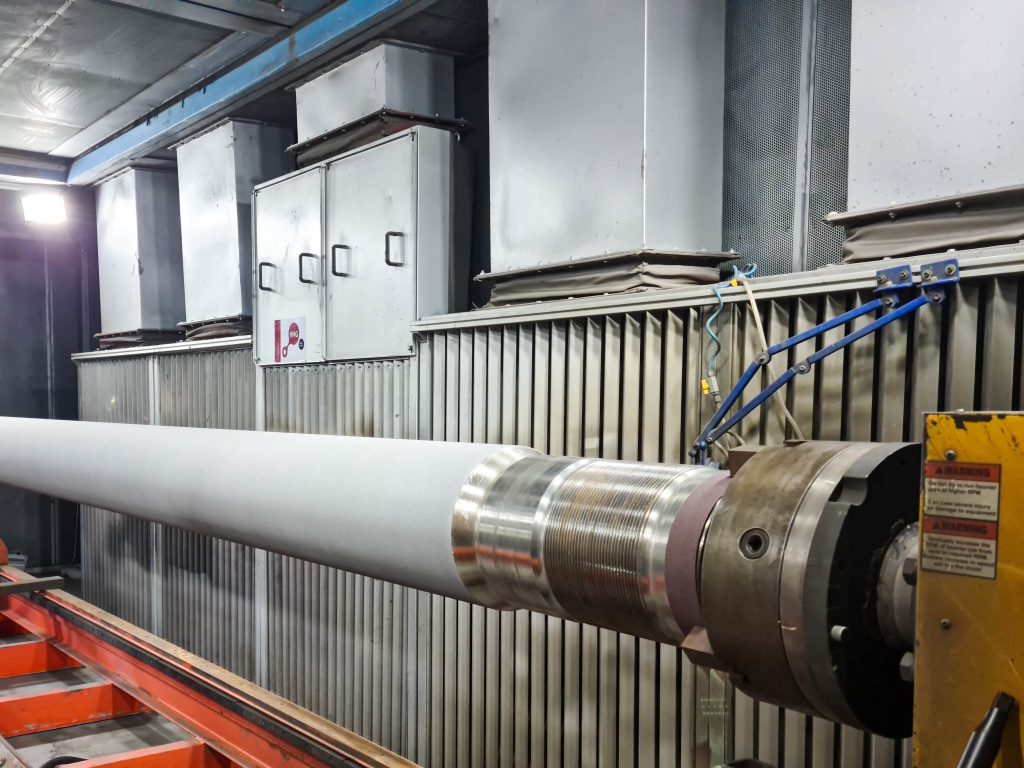
The Solution
The large capacity of HMG’s workshop meant we could carry out the manufacture of a cylinder of this size without any alterations to our work areas or machinery.
Our state-of-the-art manufacturing technology meant our engineering team were able to draft the plans of each cylinder component and program them into our CNC machinery for fast and accurate manufacture.
Each component was then thoroughly measured to ensure all dimensions were precise and minimise risk of failure or accelerated wear. With more than 60 years’ experience in the industry, HMG have become leaders in hydraulic cylinder surface finishing technologies.
As such, we were able to adapt multiple different surface finish applications to ensure successful, long-term operation of the cylinders in a harsh and corrosive dredging environment. These alterations required replacing the surface finish material on the hydraulic cylinder rod to a dual coat chrome carbide material and the standard paint spec on the cylinder was replaced with HMG’s marine spec three coat paint system.
The chrome carbide coatings were applied efficiently and evenly by our state-of-the-art HVOF robotic thermal spray system, minimising unnecessary time spent on grinding and polishing to meet sizing specifications. The coating requires applying a dual coat comprising of a nickel-based bond coat and then a single topcoat of chrome carbide.
Applying the HVOF chrome carbide surface finish instead of the standard hardchrome will result in significantly stronger bonding between the parent rod material and the surface coating, increased operating temperatures and increased wear resistance in oxidizing and extreme corrosive environments.
HMG’s marine spec three coat paint system is applied using a zinc-based primer coat, an anti-corrosive intermediate coat and then the final colour topcoat. Each coat is applied in our climate-controlled paint booth ensuring optimal temperature, humidity, and dew point, whilst also minimising surface contaminants.
Being critical spares, the components we required to be ‘install ready’ and would be stored onboard the dredge and therefore be subject to the same harsh marine environments as they would be during operation. As such, HMG packed the cylinders into engineered ship and store frames and wrapped each cylinder in anti-corrosive plastic wrap ensuring ultimate protection during storage.
HMG were not only able to offer Hall Contracting Australian made hydraulic cylinders to reduce their down time risk, but we were also able to provide them a product that’s made to last both before installation and during operation.
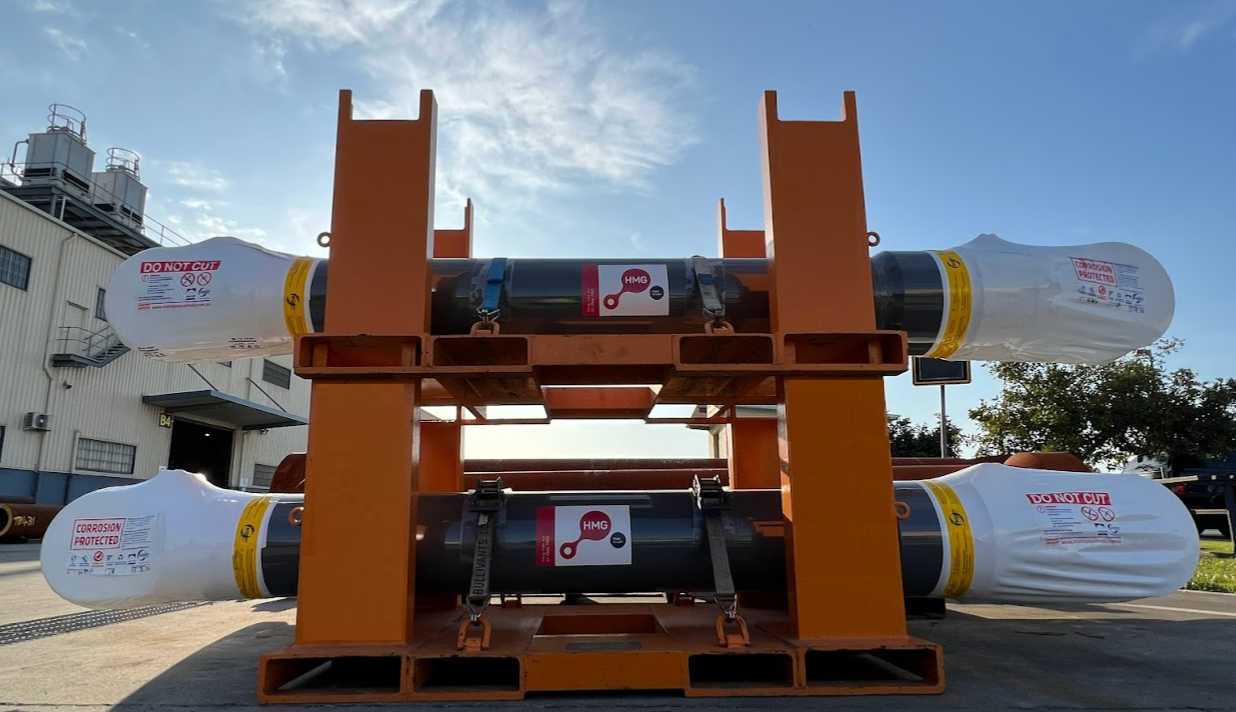