The Castlemaine Perkins XXXX brewery in Brisbane needed to refurbish the Deadslides they were using in their bottle packaging process. These Deadslides allow the bottles to be gathered from the conveyor before being pushed up to the packing station. The goal of this project was to create an exchange set of Deadslides for the XXXX Brewery’s packaging process to keep downtime at an absolute minimum. Due to the age of the machine, there were no detailed drawings available. The XXXX Brewery maintenance team requested HMG attend site and reverse engineer drawings by accurately measuring the Deadslides currently in operation. The Deadslides will be machined using state of the art CNC milling machines and manufactured from corrosion resistant food grade stainless steel, with the wear face of the Deadslides being Hardchrome plated for superior durability.
Customer problem
Castlemaine Perkins XXXX brewery’s Deadslides used in their bottle packaging process were beginning to show signs of wear as they approached end of service life. The packaging process had to be reduced by half to account for the worn slides. With the OEM of the packaging machine being based in Europe, lead times for new slides were quoted at 6-7 months. The Brewery needed replacement Deadslides on hand for scheduled maintenance in the coming weeks. They also wanted a solution that would not only meet the OEM service life but extend it if possible. With approximately 9000 bottles per hour to travel across these Deadslides, this would require a material that would not only stand up to the harsh corrosive environment, but also provide extreme durability. 316 stainless steel was selected as the material of choice, to be coated with a 125µm Hard chrome coating for superior wear resistance. The Brewery was looking for a fast turnaround without interrupting their already reduced production, meaning reverse engineering and measurements of the Deadslides would have to be taken while still installed to the machine. From the obtained measurements, detailed CAD manufacturing drawings would be created allowing for precision CNC machining of new Deadslides.
The OEM of the packaging machine being based in Europe,
lead times for new slides were quoted at 6-7 month
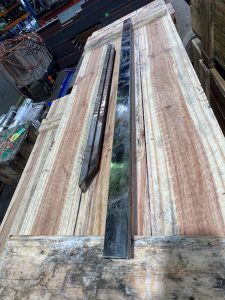
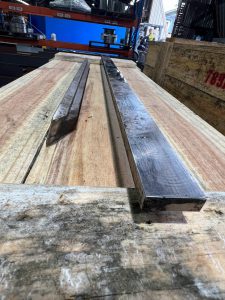
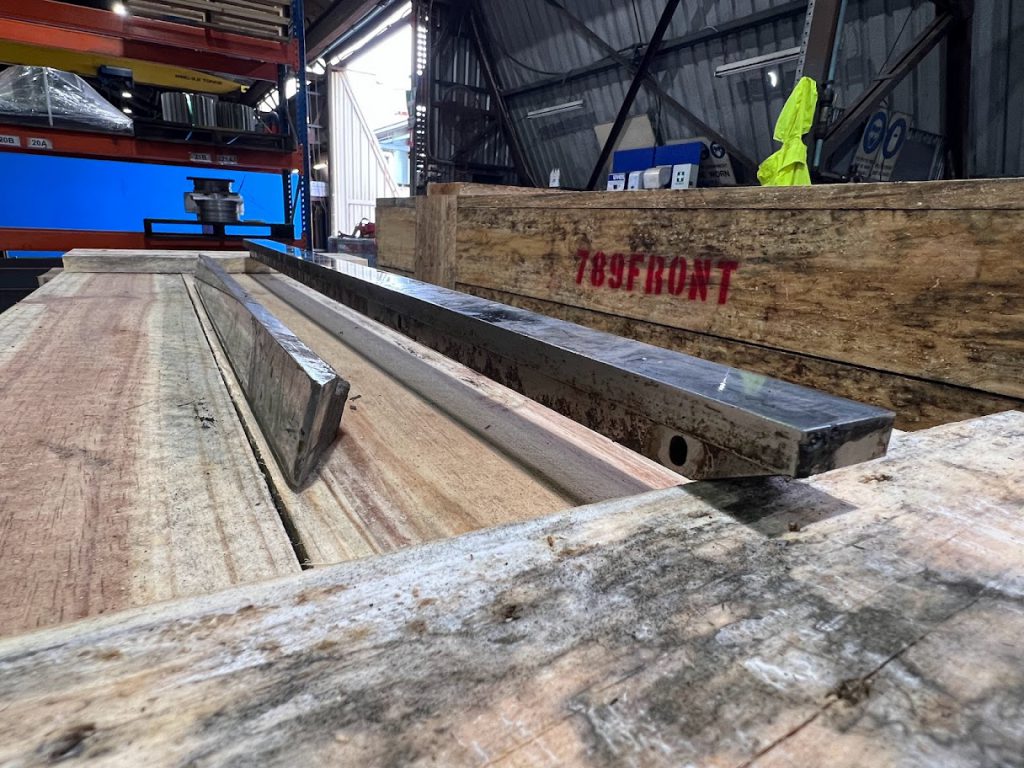
HMG Solution
With HMG’s ability to design, machine and hard chrome components in one facility, we can significantly slash lead times. Negating the need to have multiple processes outsourced guarantees our quality control officers can review the accuracy at every step of production. Our team attended the XXXX Brewery and quicky got to work taking measurements and reverse engineering the worn Deadslides. Attending site also meant the HMG engineering team could gain a full understanding of how the components need to operate and exactly what the customers’ requirements were. HMG were able to reengineer the Deadslides to include a thicker Hardchrome wear surface to significantly increase the service life from OEM recommendations. Manufacturing from a higher-grade stainless steel also increased the corrosive resistance of the slides, whilst still maintaining a cost-effective solution. The combination of CAD design, CNC Machining and HMG’s stringent quality control procedures resulted in the remanufactured Deadslides fitting first time.
HMG’s multiple CNC Machines allow us to create these custom parts. Our industrial chroming solutions are used in some of Australia’s toughest climates, we know how important high-quality chroming is to the life of a competent. We ensure our components are always Made to Last.
In total, we saved over 6 months on lead time
with the XXXX Brewery working directly with us.
Machining Process
A Deadslide is a component that is used to gather the bottles or cans from the assembly line, it needs to be accurately made and durable to ensure the uninterrupted packaging of these products. To meet these rigorous requirements, HMG machined these components out of stainless steel on our state-of-the-art Vesta 1300B CNC vertical machining centre. The Vesta 1300B has a 1300mm x 670mm table with a max Z height of 650mm. A true 4th axis attachment has also been installed on the Vesta 1300B providing 3D milling capabilities and will allow the ability to manufacture almost any design imaginable. The Vesta CNC milling centre gives the ability to make intricate and precise cuts required for the manufacture of these components. Utilizing CNC machining centres allows HMG to manufacture identical pieces quickly, we can have the order ready to go in hours, instead of days or weeks for a similar component sourced from overseas. Additionally, we keep all CAD programs onsite ready to go. If the Brewery were to require an additional set of Deadslides in the future, they would only be a phone call away.
Hard Chroming Process
Hard chroming is a process that is used to protect metal components against wear and corrosion. This is achieved by adding a surface layer of hard chrome plating to the parent metal. The hard chroming process is known as electroplating and involves firstly prepping the metal part, followed by exposure to an electric current while submerged in liquid chromium bath. We use hard chrome because it has excellent properties for use in industrial applications. It is highly resistant to wear, and corrosion and maintains excellent hardness at high temperatures and has a long life. Hard chroming also gives us more control over the thickness and uniformity of coatings than other coating systems. The hard chromed finish will help keep the new slides running smoothly without any problems.
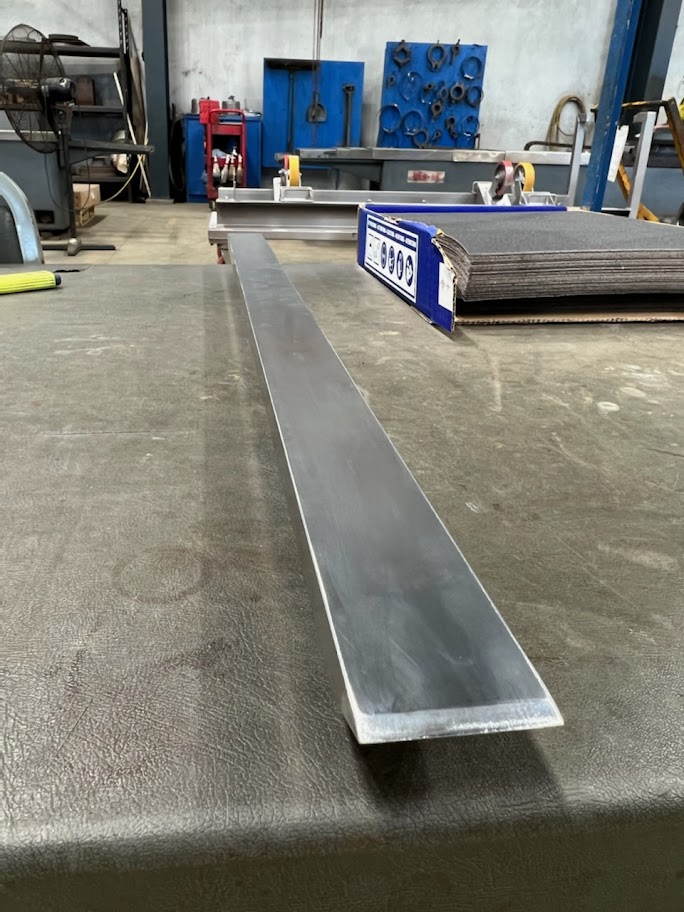
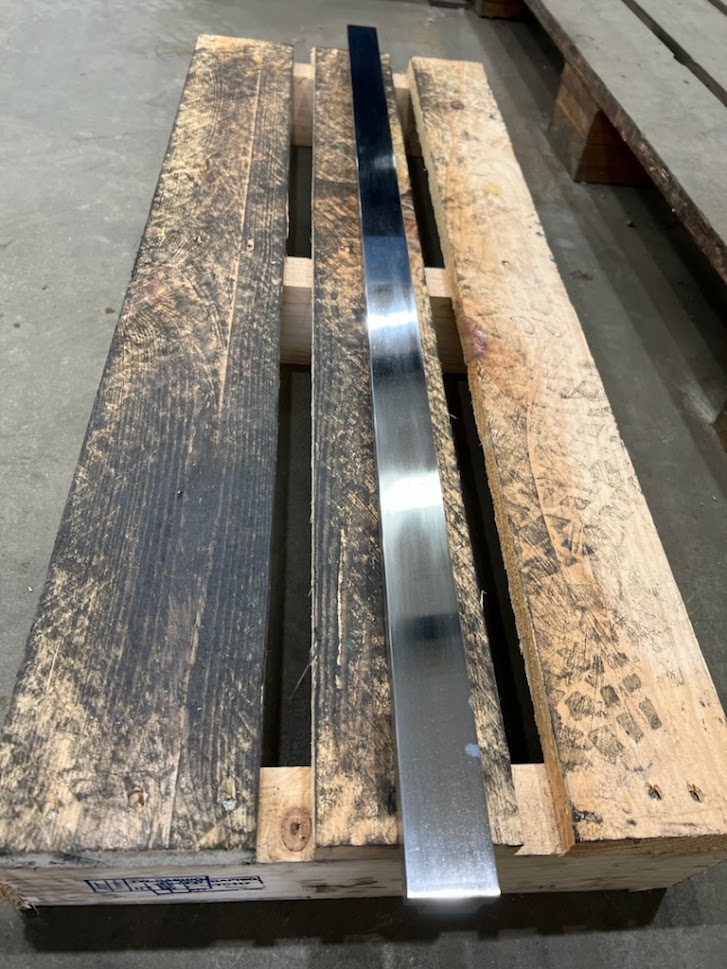
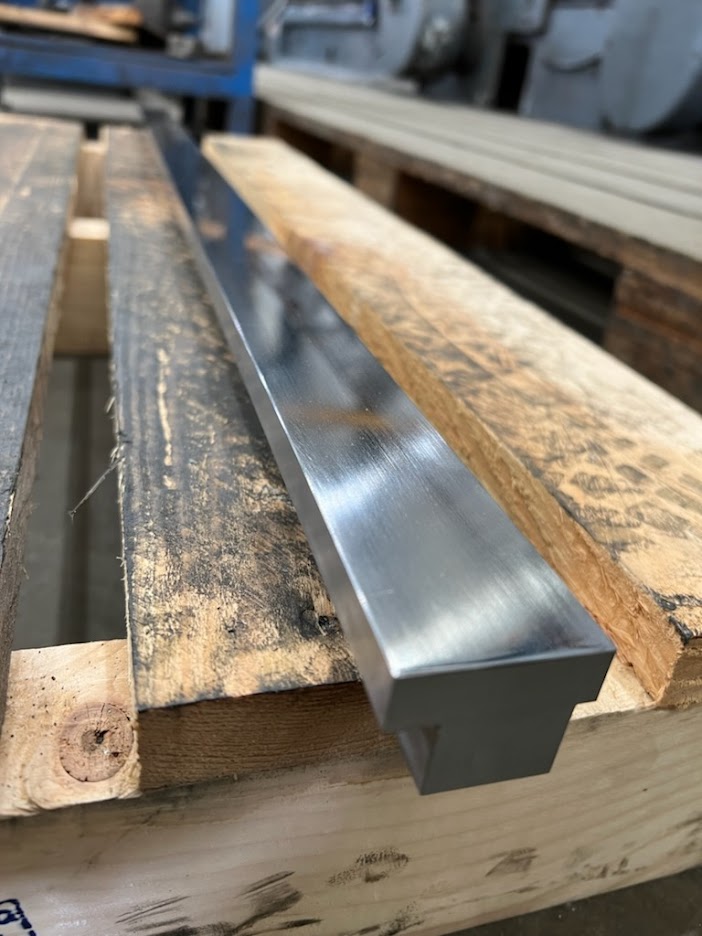
The Brewery is happy with its new components, and we’re excited to see them in use and the bottle packaging process back up to full production!