Breaking ground on a new mining project is an exciting venture, but it comes with its own set of challenges. One of the most critical challenges is preventing downtime in heavy machinery. Downtime can be costly, affecting productivity and profitability, even before you’re exporting any product.
Here are seven key measures to ensure you mitigate the risk to your machinery, your project, and your bottom line.
1. Proper Maintenance and Inspection
Regular maintenance and inspections are the foundation of preventing downtime. Develop a maintenance schedule that includes daily, weekly, and monthly checks. Ensure that all operators are trained to perform these inspections and report any issues immediately.
2. Invest in Quality Equipment
When setting up a new mine site, it can be tempting to cut costs wherever possible. However, investing in high-quality machinery from reputable manufacturers can pay off in the long run.
3. Operator Training
Properly trained equipment operators are crucial to minimising downtime. Ensure that your operators are well-trained in the operation and maintenance of the machinery they are using. Regular refresher courses and safety training can prevent accidents and equipment misuse, which often lead to downtime.
4. Implement Predictive Maintenance
Predictive maintenance is a proactive approach to preventing downtime. It involves using data and monitoring technology to predict when equipment might fail. By identifying issues before they become critical, you can plan maintenance during scheduled downtime, avoiding unexpected interruptions.
5. Maintain Spare Parts Inventory
Having a well-stocked inventory of critical spare parts is essential. When a machine does break down, quick access to replacement parts can significantly reduce downtime. Work with suppliers to ensure you have a reliable source for spare parts and keep an accurate inventory.
6. Utilise Remote Monitoring
In the digital age, remote monitoring technology can be a game-changer. These systems allow you to track the condition and performance of your machinery in real-time. When irregularities or potential issues arise, you can take immediate action, reducing downtime by addressing problems early.
7. Emergency Response Plan
Even with the best prevention measures, unexpected breakdowns can still occur. Develop a comprehensive emergency response plan that includes backup equipment, quick access to repair services, and a well-trained response team. The faster you can address an issue, the less impact it will have on your overall productivity.
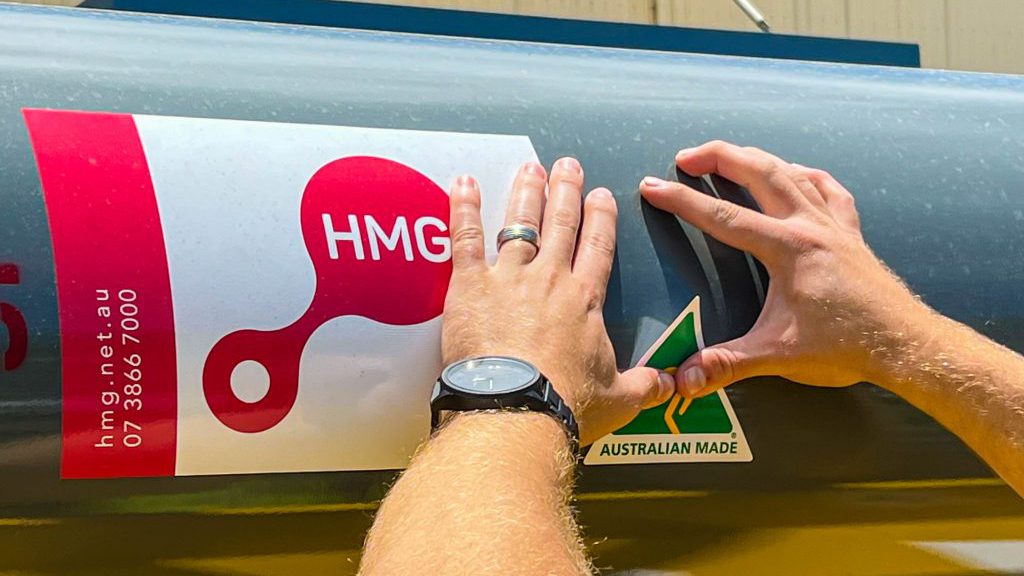
How HMG Can Help
Extensive Capabilities
At our 4,000m2 Brisbane machine shop, HMG offers comprehensive CNC machining, reverse engineering, and surface finishing services for companies across the Asia Pacific. Our large workshop facilitates controlled blasting, stripping, and inspection, ensuring product quality. We’re renowned for hard chromium electro-plating, arc spraying, and high velocity oxy-fuel spraying, serving the mining, construction, and oil and gas industries.
Quality and Safety
HMG prioritises a safe work environment, following ISO 45001:2018 standards with regular third-party audits. Our commitment to excellence is evident in our ISO 9001:2015 accredited quality management system. We also uphold ISO 14001:2015 for environmental compliance, going beyond legal requirements to protect the environment and communities.
Efficient Freight Services
HMG’s geographic reach extends to companies in Australia, Papua New Guinea, Indonesia, and New Zealand. Our advanced capabilities help reduce downtime and maintenance costs, providing door-to-door freight solutions for clients across the Asia Pacific region.
Get in touch with HMG today for all your design, manufacture and component refurbishment:
www.hmg.net.au
[email protected]
1300 509 931